CLO is to soft goods what SolidWorks is to machine parts. Game, consider yourself changed.
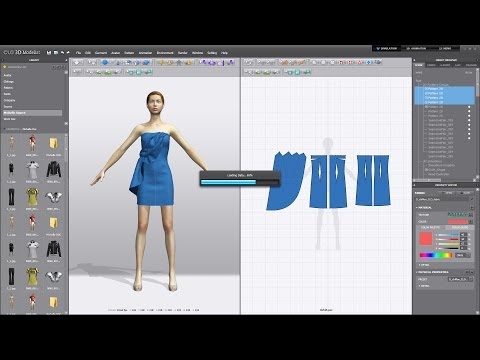
How we can illustrate this? Hmm. Ah yes…
Form-fitting Spandex Activewear. For Dogs.
You awake with clammy forehead skin, itchy fingers, and the germ of an idea that will change the world. You roll out of bed, gorilla walk across the snack food strewn floor, and wince as the piercing cold blue of ultra-bright OLED shatters the warm, musky darkness. SolidWorks.
You heave a sigh of relief as you enter your Parametric Happy Place, crack the knuckles of your sausage-like fingers, and, quietly, contemplatively, you hear yourself mutter: Maximum effort. It’s design time.
You stare blankly at the screen.
Have you ever tried to design spandex dog garments in SolidWorks? Words like “hopeless”, “asinine”, and “meat-headed” come to mind.*
* If you have actually attempted to design spandex dog garments in SolidWorks and are offended by any of the above word choices, get over it.
There have traditionally been two overarching phyla in the 3D design kingdom: Digital Content Creation (DCC) tools, and Computer Aided Design (CAD) tools. DCC’s are designed for makin’ pretty pictures for print, games, and movies. CAD is for designing hard-body objects in the real world. CAD is for designing objects in wood, metal, plastic, ceramic, glass: buildings (AEC), mechanical engineering (MCAD), and exterior shape design (Surfacing).
There is no existing category of 3D tools for the design of soft goods. Products made of wool, cotton, nylon, and Spandex are still, to this day, largely designed the old way. Designers pass 2D illustrations to skilled pattern makers, who, in turn, hand-make round after round of successive prototypes. Once a prototype is approved, its pattern can be drawn in a 2D vector drawing tool like Adobe Illustrator, then used to drive 2.5D CNC cutting machines for production. It’s slow, arduous, and, most importantly, requires a lot of guesswork, trial, and error.
Intrepid studios have long experimented with various 3D tools for soft goods design. DCC apps are favored by those who like the freedom that non-reality offers, but are then hindered by the lack of dimensional control or useful pattern output. CAD apps are typically favored by studios working with crossover products like shoes, luggage, or wearables. These products already contain elements of hard-goods design for which CAD is the perfect tool: rubber soles, wheels, plastic frames, and metal fixtures. CAD falls down, however, when asked to design the kinds of complex organic forms that Spandex demands.
CLO (big-sister to Marvelous Designer) is not a DCC, nor is it CAD. It represents an entirely new phylum. It allows users a level of fluidity, speed, and flexibility on par with that of a Visual Effects (VFX) design tool like Z-Brush, the ease-of-use on par with quasi-CAD poly modeller Sketchup, and the downstream manufacturing efficiency of a CAD tool.
With CLO, you can design soft goods around an existing 3D model, not unlike a cobbler’s last. Design patterns using simple 2D vector drawing tools, position them in 3D space, sew them together, and simulate the fall of the fabric across the last.
Most of the demos you’ll see are based around human mannequins, but you could just as easily import a dog, an iguana, or the latest MCAD data from that 9-axis robotic arm you’ve been designing. When the visual result in CLO looks good, you can export your pattern curves for the CNC cutter, and off you go.
As wearables come into vogue, we’ll need more and more tools like CLO to fill the role that CAD plays in the hard-goods world. I hope to see more of them. For now, try out Marvelous Designer. It’s free to try, and CLO really just adds pattern export features.
Do you use either? What for? And bonus if you’re using it in a workflow along with an MCAD tool like SolidWorks.